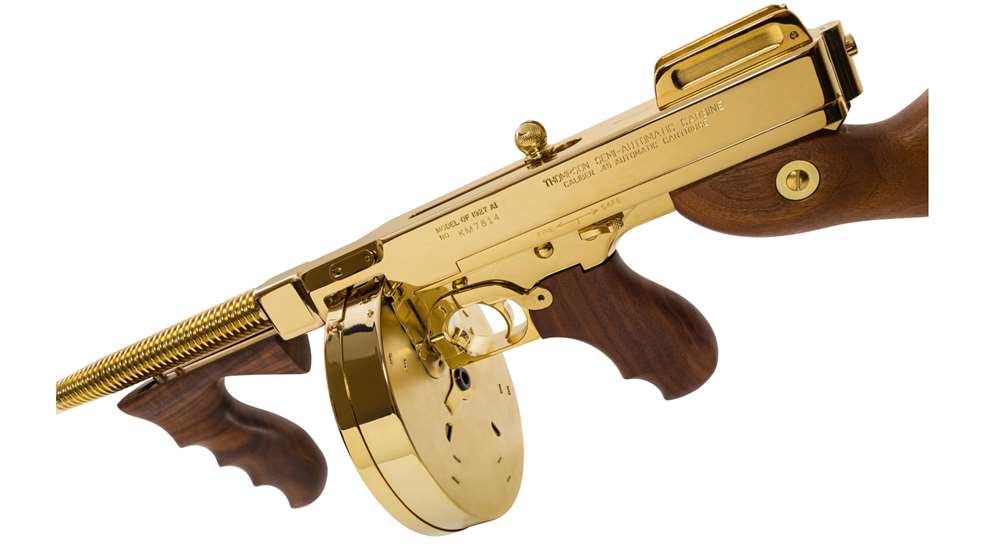
Simply stated, steel is better suited to the explosive nature of shooting than other metal or material. For this reason, rifles of every type are built using steel components including the barrels, receivers and internal parts. However, steel is comprised mostly of iron, and iron is susceptible to rust. That's why the primary purpose of all rifle finish types, or surface treatments, is to inhibit or prevent environmental oxygen and water from causing gun metal corrosion.
Today there are literally dozens of rifle finish options to choose from ranging from 19th century technology to cutting edge composites. Some are more interesting to look at while others have added physical benefits such as improved scratch resistance or increased heat tolerance. Here is a quick look at five of the popular rifle finishes you're likely to see on display at your local sporting goods store.
Black Oxide (Bluing)
Strangely enough, the popular black oxide rifle finish we all know and love, commonly called Bluing because if its blue-black color, is a close cousin of the red iron oxide we call rust. Giving gun metal a blued finish is a controlled electrochemical conversion process, or oxidizing chemical reaction, with the iron in the surface of the steel. The resulting thin layer of oxide on top of the steel increases the metal's corrosion resistance. This type of finish can be applied in various ways for different cosmetic results. Methods include Hot Bluing, Cold Bluing, Rust Bluing, Fume bluing, Niter bluing and Browning which leaves the surface with a plumy brown finish.
The much loved blued finish can have a non-reflective matte appearance or it can be polished to an eye catching shine.
Bluing is one of the oldest and most widely accepted rifle finishes in use today. For some folks, blued steel and hardwood stocks are the only way to go! A blued gun can have a non-reflective matte appearance or it can be polished to a fine shine. When properly cared for, a blued finish will easily last the lifetime of the rifle. But it's not nearly as tough or corrosion resistant as other rife finishes. It's relatively easy to scratch and offers minimal protection from rust unless it's kept dry and coated with moisture displacing oil. If you have some blued guns in storage, make sure to look them over at least a couple of times a year, especially if you live in a part of the country with higher humidity.
Parkerizing (Phosphate Finish)
Parkerizing, also known as phosphating or bonderizing, is a gun metal treatment that provides a tougher finish than bluing with an increased resistance to corrosion, nicks and scratches. The development of the phosphating process began in the 19th century in England. It was further developed by the Parker family in the United States (which is where the term Parkerized comes from). The process was adopted for the mass production of firearms by the U.S. military during World War II and it has been in use ever since.
Vintage combat rifles like the Remington M1903 and M1903A3 often have distinctive matte black or gray Parkerized finishes.
This finish is applied by dunking steel gun parts into a heated bath of phosphoric acid solution. Simmer for between 5 to 45 minutes and the components are ready to serve. Key ingredients in the solution include zinc or manganese along with various nitrates, chlorates, and copper. The resulting matte finish can have a color range from a medium gray to dark black depending on the chemical solution used. It’s a durable finish which benefits from a good coating of oil for smooth operation.
Metal Plating
Plating is a centuries old process of depositing a thin layer of one kind of metal on top of another. It's a process that's widely used in the appliance, electronics and automotive industries as well as gun manufacturing. The goal is a best-of-both-worlds result with the thin top layer, or plate, providing cosmetically desirable or corrosion resistance properties to the steel underneath. Plating can be applied to gun parts in various ways including processes that call for an electrical charge (electroplating) along with chemical or auto-catalytic processes that don't require electricity (electroless plating).
The receiver of this Henry American Beauty .22 rifle features a polished nickel finish applied over the fine line engraving.
The quality of the plating can vary depending on the preparation of the gun parts, the solutions used, and the skill of the smith applying it. The level of scratch resistance and appearance all comes down to the type of plating metal used. Nickel plated guns have been around for quite some time because nickel is corrosion resistant and it can be polished to a bright shine. Hard chrome is one of the toughest plate choices available and is commonly used to extend the working life of high velocity rifle bores.
For those who want to give their guns an artistic twist, silver and gold plating is the way to go. They offer high corrosion resistance but because they are soft metals they are best reserved for display pieces only. If you want a glittery gun you can also shoot, then take a look at a Titanium nitride finish. When polished, a Titanium-type finish provides the luster of polished gold, silver or bronze with a level of toughness similar to hard chrome.
Stainless Steel
Technically speaking, stainless steel is not a gun finish. Most finishes are comprised of a layer of material applied to the outer surfaces of carbon steel gun parts. Instead, this is a type of steel with corrosion resistance built right into it. Developed in the early 1900s, stainless steels are steel alloys which contain relativity high amounts of a mineral called chromium (at least 10.5 percent by mass) that is added for its anti-corrosive properties. Stainless steel can also be polished to a mirror shine.
The stainless steel alloys used in rifles like this Ruger 77/357 contain a high percentage of rust resistant chromium.
In most cases, a stainless-steel rifle is going to cost more than the same model with a blued finish. But it's worth the investment for guns used regularly in harsh weather conditions. Although stainless steel is a low maintenance option, it’s not a no maintenance metal. It still needs to be kept dry, clean and properly oiled. It used to be that stainless steel had an easily recognized silver appearance. But today you need to check the label because various modern coatings can be applied to stainless steel to give it a matte black look that matches polymer stocks.
Cerakote (Ceramic Coatings)
Cerakote is the brand name for a popular coating that has taken the industry by storm over the last few years. It's composed of a polymer-ceramic compound that can be air brushed onto gun parts that are then placed into an industrial kiln for a few hours to cure the coating. The result is a smooth, matte or gloss finish that is available in a wide variety of colors including black, gray, green, red, pink, blue and yellow, to name a few.
Cerakote, and other ceramic coatings, are available in a wide variety of bright or conservative colors like the Flat Dark Earth finish of this Brownells exclusive Howa 1500 barreled action.
Cerakote and similar ceramic coatings have several desirable physical qualities that make them ideal for firearms. The provide a hard, durable finish which is resistant to wear, corrosion, chemicals and impact damage. They improve lubricity, which means there's less friction between moving parts. But what gives this finish a real edge in the market place is that its applications are not limited to steel. Cerakote can be applied to a variety of materials, including wood, polymer and aluminum. This allows an entire rifle to be treated which comes in handy for matching component colors or treating the gun to a uniform camouflage pattern.